old corrugated container pulp
In the context of increasing environmental pressure and rising raw material costs, how to efficiently and environmentally convert waste corrugated paper or called old corrugated container(OCC) into new corrugated packaging paper has become a key issue in the paper-making industry. Anyang Machinery Co.,Ltd., offers a complete solution for old corrugated container pulping and new corrugated paper production, covering everything from raw material processing to finished product output. The solution includes equipment configuration, technical processes, quality control, and economic benefit analysis, helping enterprises achieve green and sustainable development. As the demand for eco-friendly packaging continues to grow, recycling and reusing old corrugated containers (OCC) has become a low-cost and highly sustainable paper-making solution.
Raw Material Sources for Corrugated Container
The raw material sources of old corrugated containers (OCC) can be divided into two main categories: virgin fiber materials and recycled fiber materials. At its core, OCC is produced by reprocessing waste cartons, cardboard, and other corrugated paper products, but its original source still depends on wood or other plant-based fibers. The following is the main sources.
Virgin Fiber Sources
- Wood: Softwood (e.g., pine, with long fibers and high strength) and hardwood (e.g., eucalyptus, with short fibers and smoothness), which together account for over 90% of the global pulp raw materials.
- Non-wood Fibers: Bamboo, bagasse (widely used in Brazil), and straw (partially used in China). Due to shorter fiber length and environmental limitations, these account for less than 10% of total usage.
Recycled Fiber Sources
- Waste Paper: Includes old corrugated containers (OCC), mixed office waste paper (MOW), old newspapers (ONP), etc. OCC is the main source for high-grade recycled paper due to its better fiber quality.
- Globally, approximately 55% of pulp is produced from recycled paper (up to 72% in Europe; China relies on imported waste paper for about 40%).
Auxiliary Materials
- Starch: Used for surface sizing to enhance strength.
- Chemicals: Such as aluminum sulfate (for pH adjustment), and wet-strength agents (e.g., PAE).
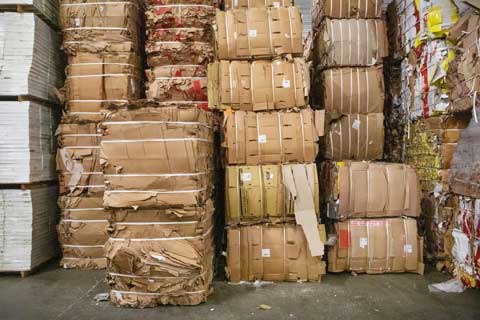
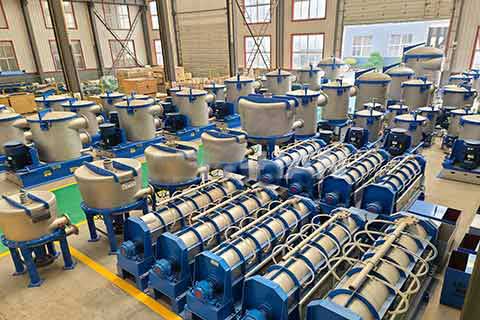
Old Corrugated Container Processing Flow
Waste OCC → Sorting → Pulping → Coarse Screening → Cleaning → Washing & Thickening → Refining → Papermaking → Drying → ReelingSorting & Pre-treatment
Purpose: Remove non-fiber impurities like plastic, tape, and metal.Equipment:
Chain Conveyor: Continuously transports waste paper to the pulping system.
Manual Sorting Table / Automatic Sorter.
Magnetic Separator: Removes metal impurities such as nails.
Hydrapulping (Disintegration)
Purpose: To disperse corrugated paper into a fiber slurry in water, forming coarse pulp.Recommended Equipment: High-consistency hydrapulper (HC Hydrapulper). High processing efficiency and low energy consumption. Combined with impurity removal devices (Ragger and Grappler) for effective removal of entangled materials.
Screening & Cleaning
Equipment:Vibrating Screen. Pressure Screen. Centrifugal Cleaner. Knotter.
Washing & Thickening
Equipment:Vacuum Drum Washer. Disc Thickener. Twin Roll Press.
Refining
Equipment:Disc Refiner. Mixing Chest.
Papermaking Section
Equipment:Fourdrinier or Multi-wire Machine. Steam Dryer Cylinder. Calender. Reeler.
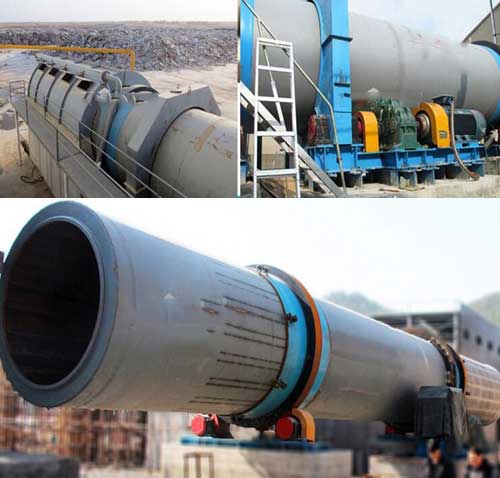
Reasons for Recycling Old Corrugated Containers (OCC)
Resource Conservation
Pollution Reduction
Economic Benefits
Policy Drivers
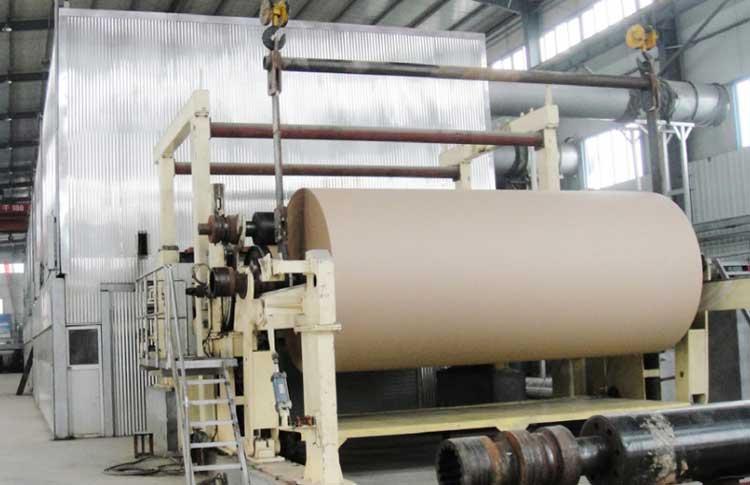
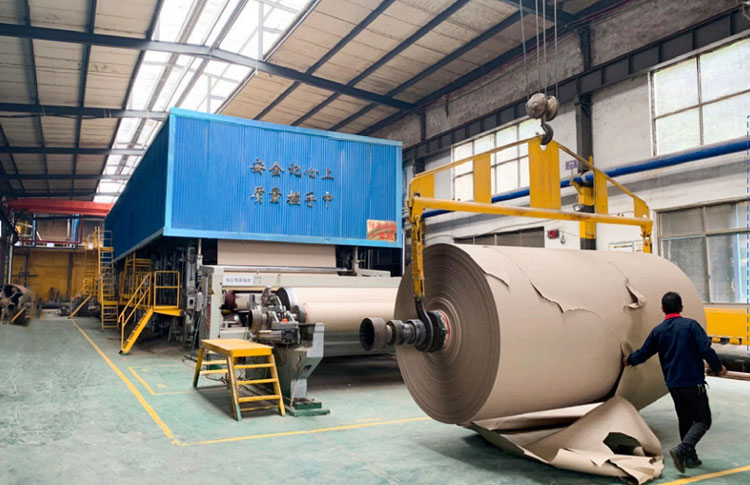
Application
The final products of occ pulp are mainly linerboard, courugated medium, packaging grade paper etc. Generally these recycled products are used for e-commerce logistics, food and daily goods packaging, appliance cushioning pakaging etc. During occ pulping process, the raw impurity rate should be lower or equal to 3%. The final paper moisture should be lower or equal to 10% and the ring crush strength should obey the GB standard.Customize OCC Pulp Solution
As a professional pulp and paper equipment supplier in China, Anyang Machinery offers one-stop turnkey solutions for old corrugated container pulp preparation and papermaking production lines. We not only supply standalone machines but also provide customized equipment models, complete with process flow diagrams during the early stage, and integrated services including on-site installation, commissioning, and staff training in the later stage. If you’re interested in a customized OCC pulp solution, please contact us for a full proposal and technical support. You are welcome to contact us for a tailored solution, including detailed process diagrams, equipment lists, and quotation information etc.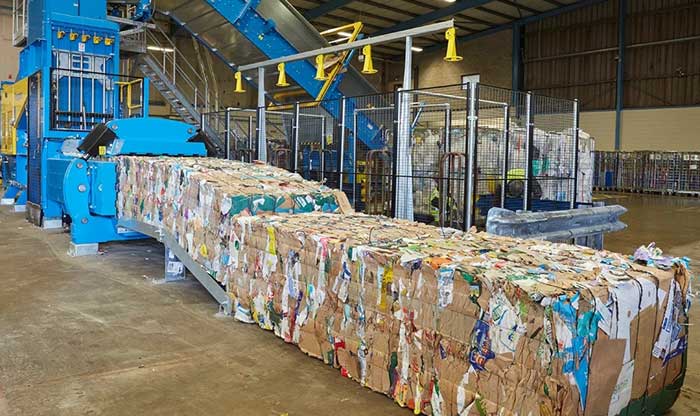
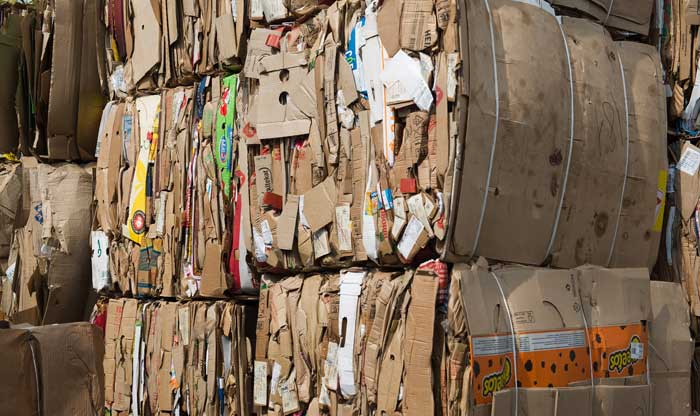