waste paper pulping
Process of waste paper recycling
The process of waste paper recycling most often involves mixing used/old paper with water and chemicals to break it down. It is then chopped up and heated, which breaks it down further into strands of cellulose, a type of organic plant material; this resulting mixture is called pulp, or slurry.
How to deal with waste paper?
In recent years, many systems have been developed for making pulp from waste paper.
After recycling, waste paper is sorted again and again, soaked in warm water, and re-pulped. Impurities in pulp are divided into two categories, one is sand and pebbles and other heavy impurities, which will form cavities and rough particles on the paper surface, the other is plastic film, colloid, dust particles and other light-weight impurities. Papermaking needs to be baked at high temperature, and these impurities will melt and stick to the paper roll when they encounter high temperature, interrupting the operation. They should be screened and purified separately.
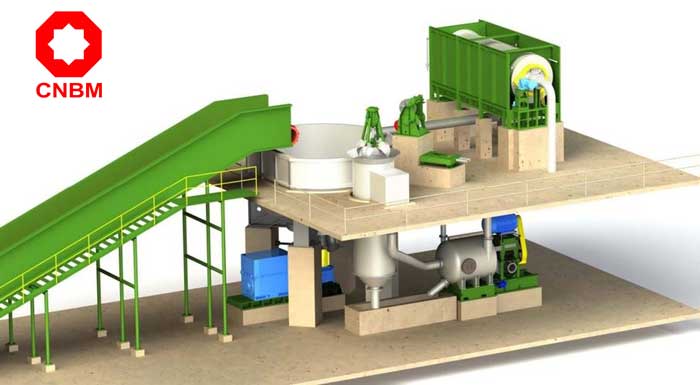
Processing of waste paper raw materials
Fiber pulp produced from waste paper raw materials, like virgin fiber pulp, must reach a certain quality before it can be better utilized. The processing system for recovered paper raw materials is usually more complex than that for virgin fibre. Waste paper pulping has different treatment processes and equipment according to the different waste paper raw materials used and the types of final products produced. Generally speaking, the treatment of waste paper includes the following steps:
- ① Sorting of waste paper.
- ② Shredding and separation of waste paper.
- ③ Screening and purification.
- ④ Deinking (except for non-deinked pulp).
- ⑤ Concentration.
- ⑥ Bleaching and beating.
The sorting of waste paper can be regarded as the pretreatment stage of waste paper, while shredding is regarded as the first step in the waste paper pulping process, and whitening and beating are to meet the final quality requirements of the pulp. In this way, the waste paper pulping process basically includes four stages of crushing, screening, purification and thickening. However, due to the wide variety of impurities contained in waste paper, especially the application of plastics, hot melts and other synthetic materials on paper products, the screening and purification in waste paper treatment is complicated. Therefore, screening and purification has become a key issue of waste paper pulping process. In this way, the entire waste paper pulping process can actually be summarized as a problem between shredding and purification. The deinking of ink-containing waste paper is a special requirement in waste paper pulping, and it is actually a purification process.
Production Process Of Making Waste Paper Into PulpAccording to the different types of waste paper raw materials and product varieties, the production process of making waste paper into pulp can be combined in many ways, which can be simply summarized into two categories. The first category is bleached deinked waste paper pulp, and the second category is natural color waste paper pulp. The waste paper pulp process basically includes four stages: crushing, screening, purification and thickening.
Waste paper pulping process, pulp products are divided into natural color paste and bleached pulp. Papermaking steps for producing primary color pulp, disintegration, cleaning, and removal of heat-dissolved waste paper. When producing bleached pulp, deinking and other treatments are added on this basis.
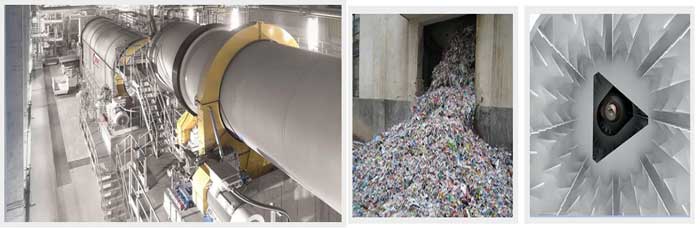
The pulping process of ordinary waste paper: 1. After the waste paper is unpacked and the iron wire is removed, it is transported by the plate conveyor to the hydropulper for disintegration. The hydropulper performs pulping and deinking on the waste paper. The pulp after ink flows into the pulp tank 2. The pulp is lifted from the pulp tank to the high-frequency vibrating screen by the pulp pump, and the high-frequency vibrating screen plays the role of screening and separating impurities; the screened pulp flows into the pulp tank 3. The pulp pump lifts the pulp from the stock tank into the rotary screen thickener. The rotary screen thickener mainly increases the low concentration of the pulp through concentration, and at the same time it can achieve the purpose of washing the pulp; the concentrated pulp inflow pool. 4. The pulp is lifted into the rinsing machine by the pulp pump, and the function is to clean the pulp and bleach the pulp; the pulp after bleaching automatically flows into the pulp tank 5. The pulp is lifted into the refiner by the pulp pump, and it is ground by the refiner. After the pulp is fine, it will automatically flow into the pulp tank. 6. The pulp pump will lift the pulp into the sand settling table, and the sand settling plate will separate impurities such as sand and ash to make pure pulp. The function of the box is to reconcile the concentration of the pulp. 8. After the pulp is conditioned by the pressure box and then removed by the sand removal pump for the second time to remove impurities, the pulp is sent to the pulp stabilization box for re-pulping to make pure pulp.
Waste paper pulping process
1. Production process of bleached and deinked waste paper pulp:
The raw material for producing bleached and deinked waste paper pulp is white waste paper, such as old newspapers, old magazine paper, old book paper, white mixed waste paper, white printing waste from printing plants, etc. The finished pulp is sent to the paper machine system to make newsprint, magazine paper, Writing paper, household paper, etc. For every ton of waste paper processed, 0.8-0.85 tons of bleached and deinked waste paper pulp can be obtained.
2. Production process of uncolored waste paper pulp:
The raw material for the production of uncolored waste paper pulp is uncolored waste paper, such as waste corrugated box, waste paper bag paper, colored mixed waste paper, waste from carton factories, etc. The finished pulp is sent to the paper machine system to make linerboard, corrugated core paper, and packaging paper , paper bags, etc. For every ton of waste paper processed, 0.85-0.9 tons of natural waste paper pulp can be obtained.
Depending on the pulping process, paper mills require different pulping machinery.
Anyang Machinery Factory is a pulp machinery manufacturer from China, we can provide both pulp solutions and stand-alone equipment for pulp production lines, such as pulp digesters, pulp machines, spray tanks, vacuum drum cleaners, twin roll presses machine, single screw press, disc press filter, pressure screen, etc. Customers can contact us at any time if they have any needs.
The thickening process increases the pulp concentration, makes the pulp easy to store, and stabilizes the pulp concentration to meet the requirements of the next process. It also saves energy consumption in pulp transportation. Washing and concentrating equipment can be divided into LC type, HC type, medium concentration type and displacement washing type according to the principle of concentration washing. Gravity disk thickeners are very common in the pulp thickening process.
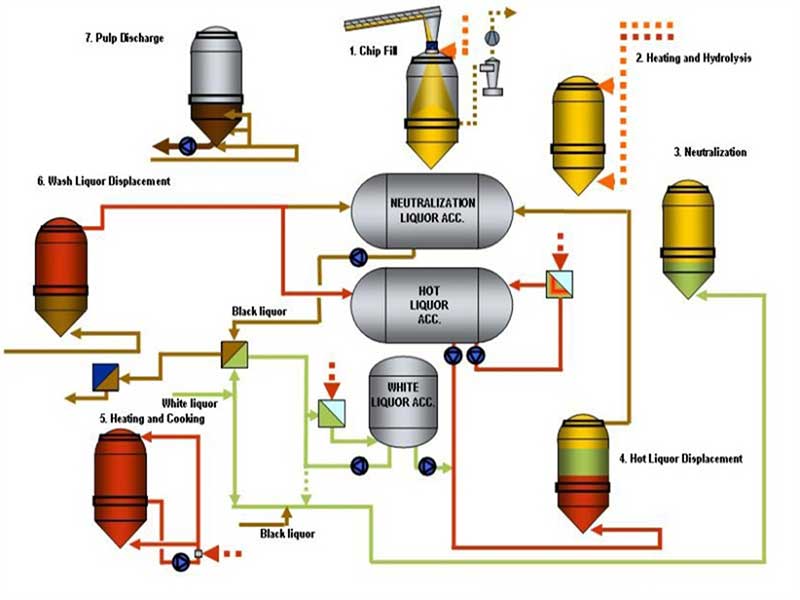
Machines for processing waste paper pulp
Commonly used shredders for waste paper pulping include hydropulpers and cylindrical shredders. The hydraulic pulper is widely used in the waste paper pulping process at home and abroad. According to the structure of the pulper, there are vertical and horizontal types, according to the operation mode, there are continuous type and intermittent type, and according to the pulp concentration, there are LC type and HC type.Screening and cleaning
Waste paper pulp screening cleaning is used to process the coarse material at the front end of the production line. In order to separate the large size impurities from the coarse pulp, the waste paper pulp should be diluted to low consistency. Commonly used equipment includes pressure screens, pressure knotters, etc.Deinking
Flotation deinking is mainly used in the production of deinked pulp. Since most printing inks are oily materials, the ink particles are hydrophobic. A surfactant is used to collect ink particles and lift them above the pulp. Flotation cell is the core equipment for waste paper pulp deinking.Wash Concentrate
The pulp washing process is to dissolve the non-fibrous soluble matter with water or diluent during the pulp cooking process, and at the same time separate it from the fiber, and finally obtain clean pulp. Generally speaking, the pulp washing process is also the process of waste liquid extraction. Common washing equipment includes vacuum drum washing machines, double-roll presses, single-screw presses, disc filters, etc.The thickening process increases the pulp concentration, makes the pulp easy to store, and stabilizes the pulp concentration to meet the requirements of the next process. It also saves energy consumption in pulp transportation. Washing and concentrating equipment can be divided into LC type, HC type, medium concentration type and displacement washing type according to the principle of concentration washing. Gravity disk thickeners are very common in the pulp thickening process.