Moulded product of paper pulp manufacturing technique
Pulp molded products usually used waste paper as a basic material in the early days, and used special equipment and molds to perform three-dimensional modeling through a unique process to produce packaging products and objects of various shapes. Here is an introduction to the production process of molded pulp products:
Pulping
Using reeds, straw husks, sugarcane, wheat straw, bamboo, wood, and recycled paper as raw materials, after crushing, grinding and other processes, they become fibers suspended in water. According to the characteristics of the final product, the fiber length and concentration of the original pulp can be controlled during the pulping process. Add functional additives (brightening agents, waterproofing agents, etc.) and dyes, and perform a series of auxiliary operations to form pulp that meets production needs.
Equipment: pulper, slurry tank, etc.
This is the most important process during making moulded pruduct of paper pulp. China National Building Materials Group Corporation (CNBM), is a key mainstay international engineering system integration service enterprise mainly involving in paper pulping machinery making.We are a supplier of pulp and paper machines. We have six production workshops to produce professional pulp and paper machines. We mainly produce digesters, disc filters, vacuum drum washing machines, two-roll press washing machines, continuous horizontal tubular digesters, thermal switches and other machines and systems. We provide a complete set of equipment for the waste paper pulp production line, the main products are multi-disc and pressurized screens; the complete set of equipment for the chemical pulping production line, which mainly includes a pulper digester and a vacuum cleaner.
Molding
The molding process of pulp molded products is mainly through a series of methods such as vacuum molding and grouting molding, so that the raw pulp fibers are formed into the shape designed by the mold, and vacuum molding is the most commonly used and most effective one.
Equipment: forming machine
Drying process
The drying process mainly uses fuel, oil, gas, electricity or steam, heat transfer oil or other media as a heat source, heating air, drying the pulp molded products in the hot air, and extracting evaporated water from the products through a fan. Accelerate the drying effect.
Equipment: dryer
Shaping and trimming process
After the pulp product is shaped and dried, it is basically shaped, and then heated with an electric heating plate or other heating medium (such as heat transfer oil) to make the pulp product mold have a higher temperature (150-250°C), and then use air pressure or hydraulic pressure, thus the paper support product is pressed under high temperature and high pressure to make the product appearance neat and beautiful, achieve better toughness, and make it have better shock resistance.
Equipment: shaping and trimming machine
Packing
Finally, the products produced through a series of processes will be inspected, packaged and stored. According to the characteristics of different products, manual packaging or automatic packaging machines can be used for counting and packaging.
Equipment: automatic packing machine
Prospect of molded product of paper pulp
The pulp molding equipment industry belongs to the environmental protection industry, and it is also in line with the development of the environmental protection industry advocated by the state. Why does it belong to the environmental protection level? Mainly manifested in three aspects:
- The raw materials used in pulp molded products are generally waste paper and other fiber products, such as waste cardboard, waste paper boxes, waste white paper, etc. The raw materials are non-polluting.
- The production process of pulp molded products is also relatively environmentally friendly. It is completed by pulp, adsorption molding, drying, and setting procedures, which is not harmful to the environment.
- The molded products made by pulp molding equipment can be recycled and reused, which further reflects the sustainable development strategy required by the country.
Therefore, through the above three aspects, it is not difficult to see that the development of pulp molding equipment meets the requirements for the development of environmental protection industries advocated by the country.
For the pulp molding equipment itself, it has many advantages that are conducive to long-term development. For example, it is extremely flexible and has strong adaptability. It can make different molded products by changing different molds, which can be developed in multiple lines. Pulp molded products also have excellent protective properties, shock-proof cushioning, compression resistance, heat dissipation and ventilation effect, the last is that the investment of pulp molding equipment is small, and the return is more. Compared with the previous packaging equipment of single mode production, it has the feasibility of simultaneous development of multiple production lines, and only needs to replace the corresponding product mold.
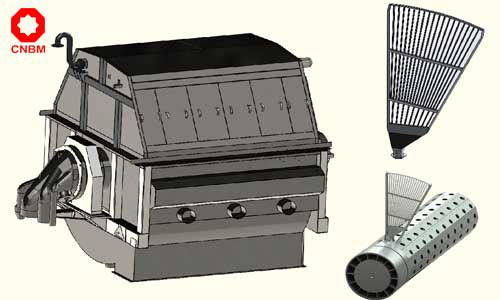
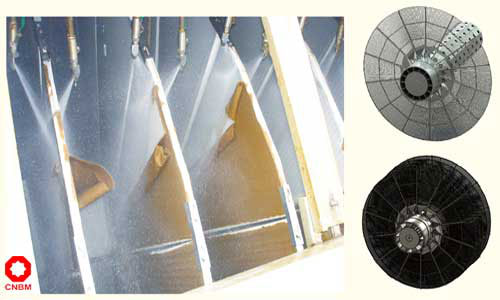
As a result, the development prospects of pulp molding equipment are obvious.
As stated, pulp moulding equipment becomes more and more popular, among all the processes, pulping is the first and quite important one. For the details of pulping, cooking, screening and washing are the necessary procedures. What’s more, besides waste paper, bamboo, wood, bagasse and cotton are the perfect raw materials of pulping. We also offer all the pulping machines, welcome to contact with us!