Membrane treatment technology to realize zero discharge of pulping wastewater
About zero discharge of pulping wastewater
As the second prize of the National Science and Technology Progress Award, the award-winning project "Membrane Preparation, Integrated Technology and Application for Zero Discharge of Pulping Wastewater" was completed by Professor Xing Weihong from Nanjing University of Technology, aiming to achieve zero discharge of pulping wastewater and comprehensive utilization to it. This article mainly introduces the key innovations of the project.
The traditional pulp and paper industry is an industry with high water consumption and high emissions. Among them, the pollutant composition of pulping wastewater is complex, and it is difficult to realize the recycling and utilization of wastewater. Most of them are discharged into the sea and rivers after meeting the standards. In 2012, due to the problem of the discharge of pulping wastewater from a company in Jiangsu Prince, make a serious result, and there was an urgent need to achieve zero discharge and comprehensive utilization of pulping wastewater through science and technology.
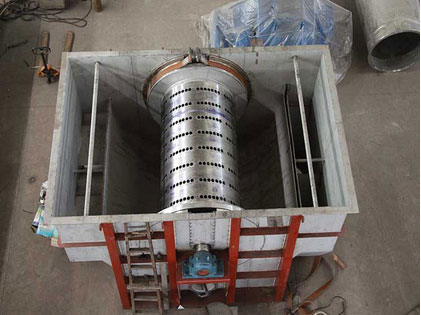
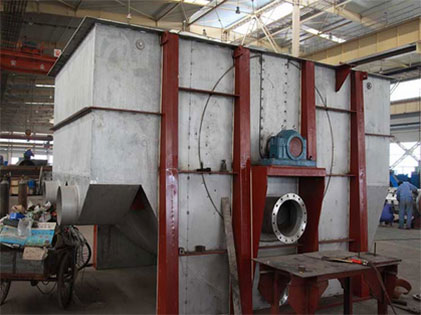
Membrane treatment technology to realize zero discharge of pulping wastewater
In response to this major demand, the Xing Weihong project team developed a new technology for zero discharge of pulping wastewater with multi-membrane integration as the core, and realized the resource utilization of pulping wastewater. In 2014, the world's first set of membranes of 40,000 tons/day was implemented. The demonstration project of zero discharge of waste water from the method of pulping has solved social development problems with scientific and technological means. With the support of national science and technology projects, the key technologies for zero discharge of pulping wastewater based on the preparation of core membrane materials, membrane pollution control, and multi-membrane integration processes have been overcome, and the following innovations have been formed:
- Invented an amphiphilic copolymer film forming method, developed a super-hydrophilic high-strength special ultrafiltration membrane, and realized industrial production and large-scale application. Creatively introduce the amphiphilic copolymer with polyvinylidene fluoride (PVDF) as the main phase into the PVDF homopolymer casting solution to make the hydrophilic components migrate to the membrane pores and surface during the film formation process, resulting in spontaneous hydrophilic properties. By adjusting the entanglement between molecular chains, the membrane material has permanent hydrophilicity, through the coupling of vapor-induced phase separation and non-solvent-induced phase separation processes, the precise control of the ultrafiltration membrane microstructure is achieved, and the pulping is solved in wastewater treatment, the ultrafiltration membrane is prone to pollution and broken filaments, which improves the operation stability.
- Developed the water quality softening and reverse osmosis membrane pollution synergistic control technology, which improved the water recovery rate of the reverse osmosis membrane and prolonged the membrane cleaning cycle. Invented the method of membrane pollution control and cleaning for high-salt system, established the relationship between reverse osmosis membrane screen and membrane separation performance, invented the method of alkaline lignin modified reverse osmosis membrane, and improved the ability of reverse osmosis membrane to resist pollution. Developed water softening and reverse osmosis membrane pollution synergistic control technology, increased the water recovery rate of reverse osmosis membrane from 70% to more than 90%, reduced the consumption of reagents in the desalination process of reverse osmosis membrane by 40%, and solved the use of reverse osmosis membranes in industrial wastewater. The problem of low water recovery rate in the treatment process effectively reduces the operating cost of the membrane system.
- Taking multi-membrane integration as the core, invented the technology package of membrane pulping and papermaking wastewater zero discharge technology, and implemented the world's first membrane pulping wastewater zero discharge project. According to the production method of chemical products, make full use of pulping tail water, invented "efficient pretreatment-multi-membrane integration-efficient evaporation and crystallization" and other pulping wastewater resource treatment technology package, implemented in Nantong. The zero-discharge project of pulping wastewater with a 4000ton/day treatment scale obtains by-products such as purified water, industrial salt and dry mud, and realizes resource utilization. The project investment cost and operating cost are about 50% of the original sea drainage project. Such bad incident was solved with technology, and it has been fully affirmed by the party and state leaders, governments at all levels and all sectors of society.
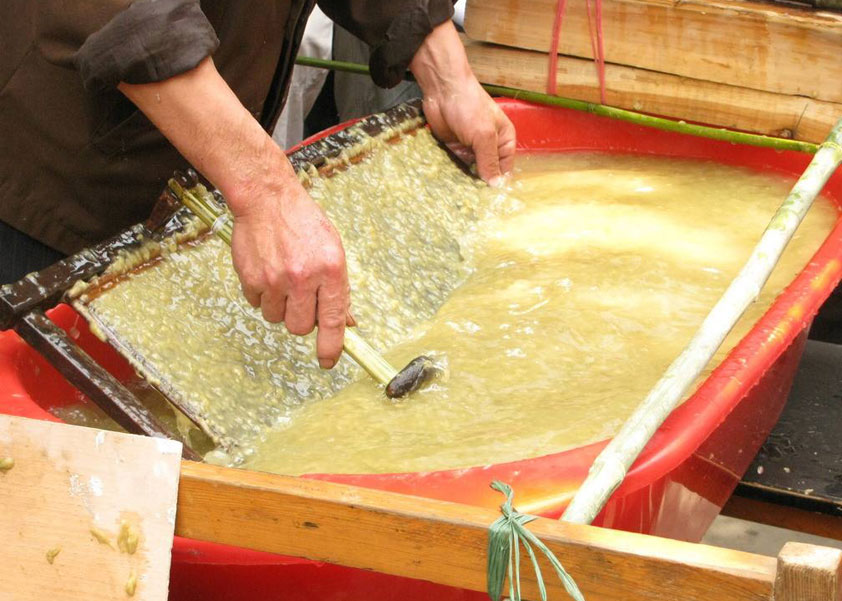
During the implementation of the project, 30 Chinese invention patents were obtained and 22 papers were published. The accumulative new output value of the transformation of unit project achievements exceeded 400 million. It was promoted and applied to pulp and paper, chemical, printing and dyeing, non-ferrous and other industries, and the total emission reduction of wastewater was 130 million tons, which produced significant economic benefits.
We all know it is important to solve the wastewater when pulping. During the process, CNBM can offer different kinds of models of machines to meet the requirements of customers. Among the machines, gravity disc thickener is quite important, besides gravity disc thickener, we can offer high quality machines for pulping cooking, screening and washing. Hope to build business cooperation with customers all over the world!
Technical parameters of gravity disc thickener
Model Item | ZNP26 | ZNP35 |
Dia. (mm) | 2600 | 3500 |
Per-disc filtration area (m2) | 7.5 | 15 |
Capacity |
0.8—3t/m2.d
0.3-2 |
|
Inflow consistency (%) | 0.3-2 | 0.3-2 |
Outflow consistency (%) | 3~5 | 3~5 |
Washing pressure for sieve cleaning (Mpa) | 0.6-0.7 |